Experience professional quality made easy by Shirt Printing Center Transfers: the leading custom DTF Transfers provider in the industry.
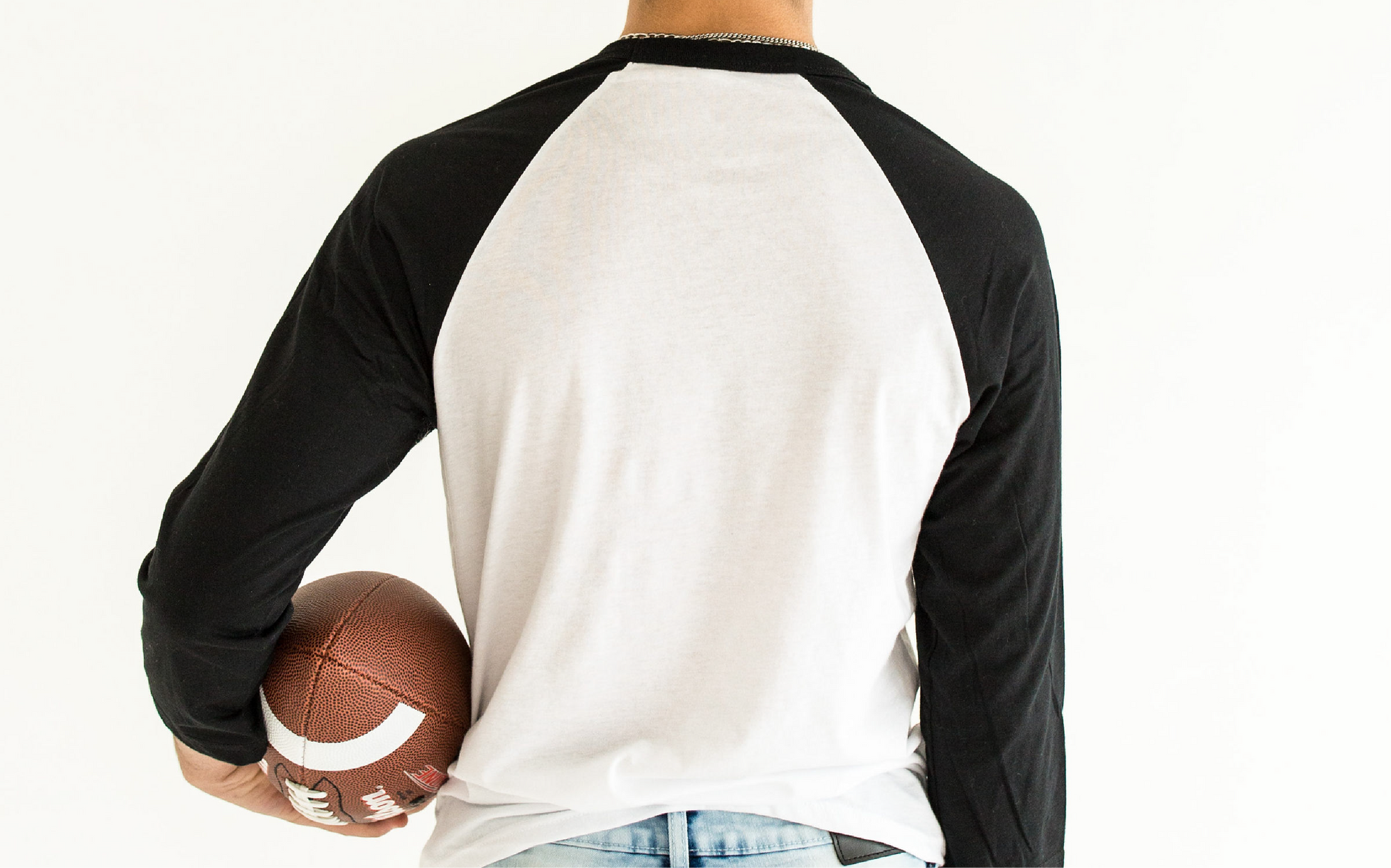
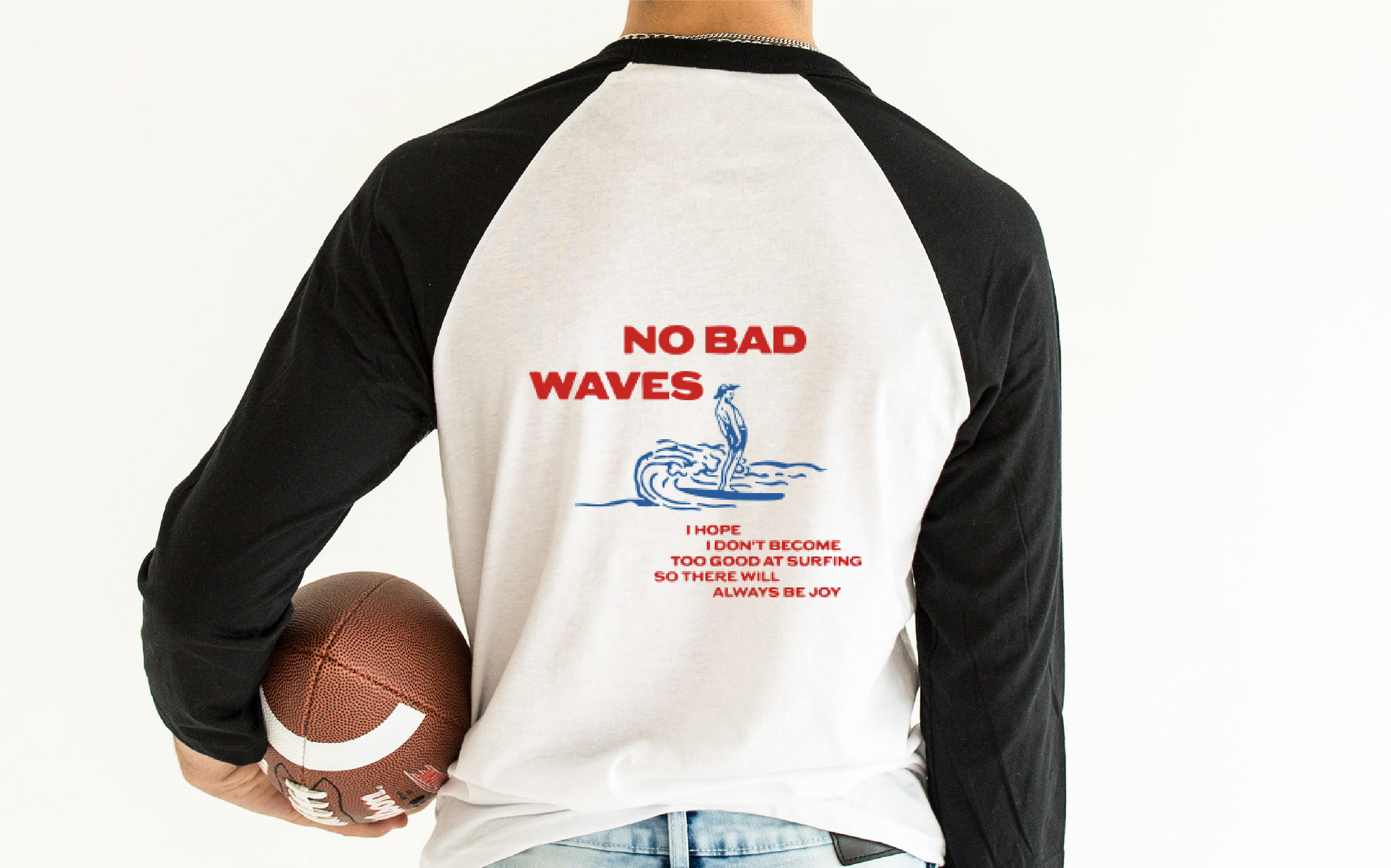
TIPS
Upon delivery, apply your DTF transfer at 320°F /160°C with medium pressure for 12-15 seconds on your chosen surface. Let it cool for 15 seconds, peel, and press again for lasting durability.
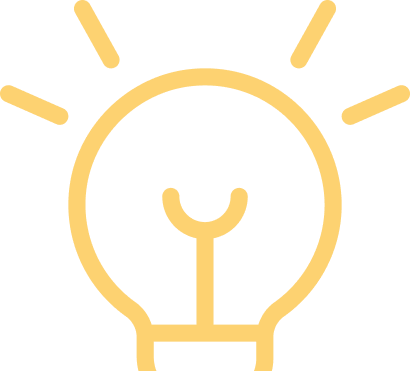
FAQs
DTF Transfers (Direct-to-Film transfers) are an innovative printing method used to apply designs onto various fabrics. Unlike traditional screen printing or vinyl methods, DTF transfers allow for full-color, detailed images to be transferred with ease. The process involves printing a design onto a special PET film using DTF inks. The printed film is then coated with a hot melt powder, which acts as an adhesive between the film and fabric. This method is highly versatile, enabling prints on a wide range of materials, from cotton and polyester to blends and even non-traditional surfaces like leather. DTF transfers are known for their durability and vibrant color reproduction, making them a popular choice for custom apparel and accessories
To create DTF transfers, you need a few essential materials: a DTF printer, special DTF inks, PET transfer film, hot melt powder, and a heat press. Begin by designing your artwork using graphic design software. Print the design onto the PET film using a DTF printer equipped with DTF inks. Immediately after printing, sprinkle hot melt powder onto the wet ink. This powder acts as an adhesive when heated. Shake off any excess powder to ensure a smooth application. Cure the transfer by placing the film in an oven or under a heat press at a low temperature for 2-3 minutes. Once cured, your DTF transfer is ready to be applied to fabric using a heat press set to the correct temperature and time settings.
Pressing DTF transfers involves using a heat press to transfer the design from the PET film onto the fabric. First, preheat your heat press to 320°F (160°C). Place the fabric on the heat press platen, then position the transfer film with the printed design facing down on the fabric. Cover with a Teflon sheet to protect the design. Press the transfer with medium pressure for 15-20 seconds. Once the pressing time is complete, carefully remove the fabric from the press and allow it to cool completely. After cooling, gently peel off the PET film. The result is a vibrant, durable design that’s soft to the touch and can withstand multiple washes.
Printing DTF transfers requires a DTF printer and specialized DTF inks. Start by creating your design on a computer using graphic design software. Load the PET transfer film into the DTF printer. Ensure the printer is set up to use DTF inks, which are designed to adhere to the transfer film and provide vivid color output. Print the design onto the film, ensuring high resolution and accuracy. After printing, immediately apply hot melt powder to the wet ink to prevent smudging and ensure the design adheres well to the fabric. The printed film is then ready for the curing and heat transfer process.
To apply DTF transfers, start by ensuring your heat press is preheated to 320°F (160°C). Place the garment flat on the heat press platen. Position the printed and cured transfer film onto the garment with the design facing down. Cover with a Teflon sheet to protect both the transfer and the fabric. Close the heat press and apply medium pressure for 15-20 seconds. Once the time is up, open the press and carefully remove the garment. Allow it to cool completely before peeling off the PET film. This cooling step is crucial for ensuring the design adheres properly to the fabric, resulting in a high-quality, long-lasting print.
You can purchase DTF transfers from various online retailers and specialty stores that focus on printing supplies. When buying DTF transfers, consider factors such as the quality of the transfer film, the durability of the ink, and the reputation of the supplier. High-quality DTF films and inks will ensure better adhesion, vibrant colors, and a longer-lasting print. Many suppliers also offer bulk purchasing options, which can be cost-effective for businesses. Look for suppliers with good customer reviews and those who provide support and instructions on using their products.
The ideal pressing time for DTF transfers is typically between 15-20 seconds at 320°F (160°C). However, this can vary depending on the type of fabric and the specific transfer materials used. It’s important to follow the manufacturer’s instructions for both the transfer film and the fabric type to achieve the best results. Applying the correct pressure and time ensures the transfer bonds well with the fabric, resulting in a durable and vibrant print. Under-pressing or over-pressing can lead to issues like poor adhesion or fading colors.